6" x 6" x 13/16"AKYAPAK AKD 160 ANGLE PROCESSING LINE
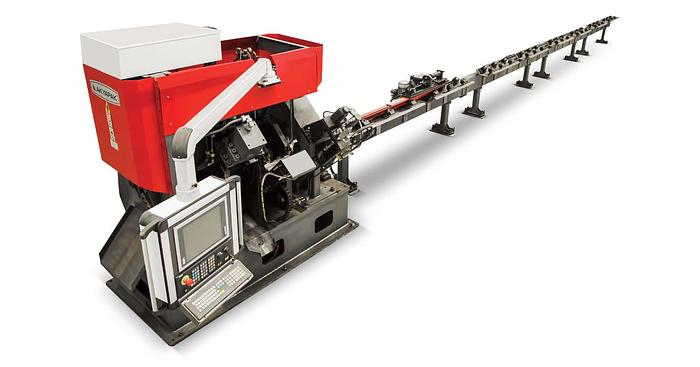
6" x 6" x 13/16"AKYAPAK AKD 160 ANGLE PROCESSING LINE
Contact us for price
Location:Florida
Description
▪ AKD 160 ANGLE PROCESSING LINE
▪ Punching Unit – 2 units, 3 punching tools per unit
▪ Marking Unit – 8 cartridges, 8 letters and numbers per cartridge
▪ Shearing Unit – 275 ton hydraulic piston
▪ Infeed system – 40 feet, feeding arm, infeed roller conveyors, material preloading tables, automatic material loading arm
▪ Outfeed system – 40 feet, driven rollers, outfeed roller conveyors, finished part platforms
▪ Material refencing system
▪ Automatic lubrication for the infeed system
▪ Siemens Simotions Controller
▪ AKD Designer
▪ DSTV file import
PUNCHING UNIT
Special design robust hydraulic 100-ton pistons with leak-proof characteristic, which are resistant to high pressure, performs punching with speed and accuracy. Three punch stations for per hydraulic unit performs shaped holes such as squares, rectangles and slots.
Improved punch tool design enables for easier and quicker punch tool and die changes.
MARKING UNIT
Hydraulic cartridge marking unit is provided as standard. 8 characters including letters and numbers are available on a cartridge. 8 cartridges can be placed into the marking system. 8 numbers or letters on a cartridge are pressed all at once. The system marks a cartridge with 8 characters approximately in 4 seconds. The cartridges are accurately positioned by servo motor. The marking results are of high readable quality even after painting or blasting processes.
SHEARING UNIT
Manufactured with high precision, the shear’s blade cuts metals with a single stroke by a 275-ton piston accurately. The blade can be adjusted according to angle size
INFEED SYSTEM
Feeding arm
The feeding arm with gripper carries out longitudinal positioning of materials. The precise motion ability is guaranteed with a servo driven rack and pinion system. The positioning accuracy in 40 feet is only ±0.04".
The profiles can either be driven forward and backward. Gripping thickness is from 3/16" to 13/16" based on the material. Max. speed 2.55 inch/min
The positioning system is not effected by scale, rust and weather conditions and is therefore more accurate. Further, the feeding arm system allows for processing with less wastage compared to roller systems.
Materials are moved through the machine by the feeding arm on sturdy roller conveyors. Standard infeed line is provided for 40-feet materials.
Material preloading tables
Materials placed on the pre-loading tables are moved to the infeed conveyors automatically by chain system driven by motor+reducer. The sensors on the system detects material position and ensures continuity of the process. The pre-loading tables can store and move automatically up to 5 materials.
Automatic material loading arm
The loading arm transfers materials from the pre-loading tables to the infeed conveyors automatically, eliminating manual intervention.
OUTFEED SYSTEM
The driven outfeed rollers moves materials to the outfeed conveyors. The outfeed conveyors turn right or left and processed parts are easily moved to the finished part platforms. The materials shorter than 20" * are cut and fall down in a bin.
* The length of the small part can be extended upon request.
MATERIAL REFERENCING
Laser sensors placed on the machine recognize materials moved by the feeding arm and the machine automatically references the material. Accurate material measurement is also ensured by the referencing system.
AXIS MOTIONS
The roller linear guidance system, which provides high rigidity and a load carrying capacity, is employed in the motion axes. This system supports all loads and moments from all directions. These components are chosen from high quality INA – Schaeffler Group® (Germany) products or the equivalents. Accurate positioning and high feed rates are guaranteed with servo motor driven ball screws. Components of the rack and pinion system are chosen from Atlanta® (UK), Schneeberger® (Germany), WHM Herion® (Germany) or the equivalents.
AUTO-LUBRICATION
The centeral lubrication system consists of a grease pump and main and intermediate distributors. Lubrication points in the feeding group including linear guides are lubricated automatically and periodically by this system.
ELECTRICAL COMPONENTS
All critical electrical components used in the system such as thermic, contactor, relay, etc. are chosen high quality products by well known brands such as below or equivalents.
CONTROLLER
Merging performance and modularity
SIEMENS SIMOTION, the proven high-end motion control system, features optimal performance for all machine concepts as well as maximum modularity. The SIMOTION further optimizes its benefits with regard to modularity, openness, and efficient software development. It combines powerful hardware with efficient engineering and innovative software. The SIMOTION enables CNC to be Integrated with sequence, motion, and robot automation systems.
Key Features
• Accelerated communication speed over the inter-CPU shared memory
• 15” Touch screen Monitor- HMI
• Profinet benefits, including noise free, 100Mbps communication
• Ability to resume operations in case of electric power cut-off.
• USB port for program backup
AKD DESIGNER
The AKD Designer is designed by Akyapak to provide super easy operation of the machine. The AKD designer features user-friendly interface and intuitive design which allows for powerful programming options. The AKD designer is customizable to meet the unique needs of the customers. The AKD designer provides auto-nesting module for maximized processing efficiency. The parts are easily previewed as 3-D in the program. The AKD Designer is equipped with versatile modules to import, modify, create and export part programs. DSTV files are imported into the AKD Designer for editing or CNC file creation.
CE AND INTERNATIONAL STANDARDS
All Akyapak Angle Lines are in compliance with CE regulations and meet the following international standards.
Related Directives and Annex: Machinery Directive 2006/42/EC/Annex VIII, Low Voltage Directive 2014/35/EU.
> EN ISO 12100:2010 - EN 60204-1:2018
SERVICE AND SPARE PARTS
With dedicated, specialized and experienced teams, Akyapak is with you even it cannot be with you to provide unparalleled technical and spare part services whether on-site or remote:
▪ On-site installation, training and consultancy service by qualified teams of expert
▪ Quick solutions without loss of time thanks to spare part stocks
▪
Instant error diagnosis, data analysis and support*
▪ Remote support with augmented reality technology through smart phone, tablet and smart glasses**
* Broadband internet connection is required for online services. The ethernet connection shall be provided by the customer to where the machine is installed.
** Remote service with wearable augmented reality AUG is optional.
Specifications
Manufacturer | AKYAPAK |
Model | AKD 160 ANGLE PROCESSING LINE |
Condition | New |
Stock Number | Factory |
PUNCHING AND SHEARING | Technical Specifications |
Number of punching units | 2 Units |
Number of punching tool | 3 tools per punching unit |
Punching power for each unit | 100 Tons |
Max. punching diameter (59,000 PSI) | 1-1/4 Inch |
Max. punching thickness (74,000 PSI) | 13/16 inch |
Max. shearing power | 275 Ton |
MATERIAL | Specifications |
Max. material size | 6.3 x 6.3 x 13/16 Inches |
Min. material size | 1-1/2 x 1-1/2 x 3/16 inch |
Max. material length | 40 feet |
MARKING UNIT | Specifications |
Total power | 94 Tons |
Marking type | Cartridge system |
Number of catridges | 8 |
Number of characters | 8 per catridge |
Character dimensions | 0.39" x 0.47" x 21 ga.0.39" x 0.47" x 21 ga. inch |